Predictive Maintenance für Großindustrieanlagen auf Basis von Sensordaten
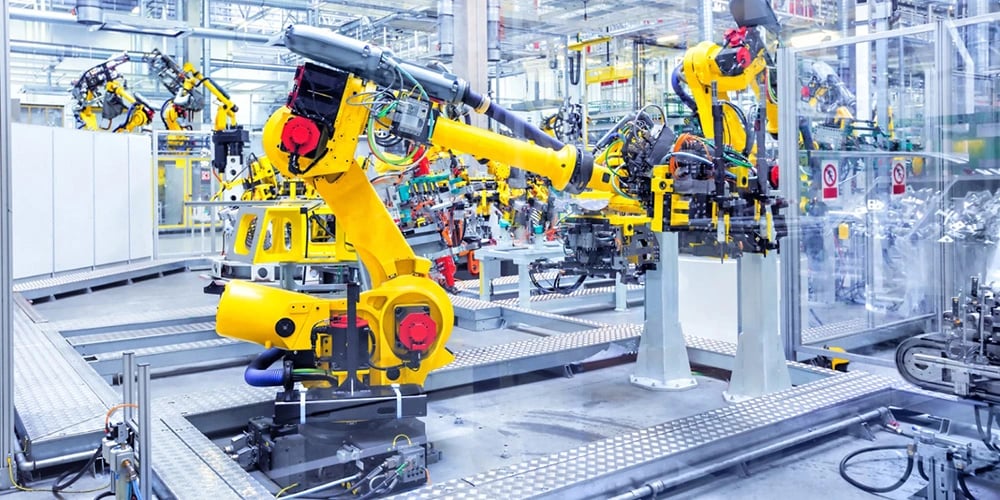
Durch Ausfälle von Großindustrieanlagen erlitt unser Kunde einen erheblichen wirtschaftlichen Schaden. Um diese Störfälle frühzeitig zu erkennen entwickelten wir gemeinsam eine Predictive Maintenance Lösung zur Echtzeitanalyse von Sensordaten seiner Anlagen, die die frühzeitige Prognose von Wartungsbedarf und ungeplanten Ausfällen einzelner Anlagenkomponenten ermöglicht. Dadurch können Wartungsarbeiten nach Bedarf gesteuert, Instandhaltungskosten gesenkt und ungeplante Ausfälle vermieden werden.
Wirtschaftlicher Schaden durch Anlagenausfälle
Obwohl unser Kunde seit Jahren große Mengen an Sensordaten von den Maschinen seiner Produktionsanlagen speichert, werden die Anlagen entweder reaktiv oder in fixen periodischen Zeitabständen gewartet. Dadurch entsteht ihm durch ungeplante Ausfälle und unnötiges Wechseln von funktionstüchtigen Bauteilen ein erheblicher wirtschaftlicher Schaden. Um diese Mehrkosten zu verringern war das Ziel einen präventiven Wartungsansatz zu entwickeln, der Ausfälle frühzeitig erkennt und Wartungsbedarf planbar macht.
Predictive Maintenance zur frühzeitigen Erkennung von Störfällen
Im Rahmen des Projektes haben wir zunächst gemeinsam mit dem Kunden einen geeigneten Ansatzpunkt für Predictive Maintenance identifiziert. Eine Schwierigkeit war, dass es durch die geringe Anzahl und hohe Diversität der Störfälle kaum wiederkehrende Muster für Anlagenausfälle gibt. Daher war die Anwendung von klassischen Musterkennungsansätzen zum Identifizieren von kritischen Zuständen und nahenden Ausfällen nicht möglich.
Deshalb haben wir in enger Zusammenarbeit mit Fachexperten eine Predictive Maintenance Lösung basierend auf der kontinuierlichen Überwachung des Gesundheitszustands der Anlage entwickelt.
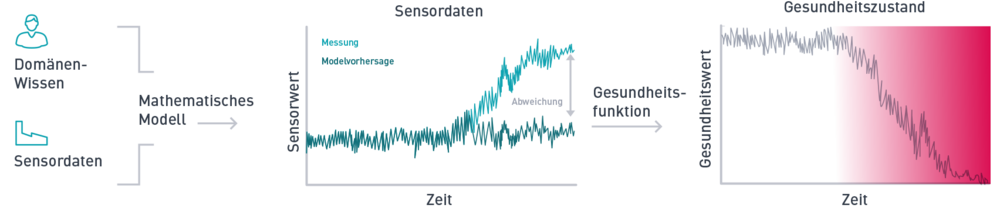
Abbildung: Schematische Darstellung der Predictive Maintenance Lösung
Hierfür bereinigten wir zunächst die in Echtzeit vorliegenden Sensordaten der Anlagen und synchronisierten die heterogenen Zeitreihen der einzelnen Sensoren. Im nächsten Schritt nutzten wir die aufbereiteten Daten, um die erwarteten physikalischen, thermodynamischen Interaktionen verschiedener Parameter der einzelnen Maschinenkomponenten wie beispielsweise Drücke, Temperaturen oder Schwingungen, zu modellieren. Abweichungen zwischen den physikalischen Modellen und den aktuellen Sensordaten, sogenannte Anomalien, wurden genutzt, um den Gesundheitszustand der Anlage zu prognostizieren.
Diese Predictive Maintenance Lösung wurde in einem Projekt mit Echtzeitdaten bei unserem Kunden operationalisiert und erfolgreich getestet. Dabei konnten wir verschiedene bekannte historische, aber auch neue Störfälle oft Wochen vor einem Ausfall identifizieren.
Bessere Planung von Wartungsarbeiten und Reduktion von Ausfällen
Durch die Überwachung des Gesundheitszustandes einzelner Anlagenkomponenten können Ausfälle frühzeitig erkannt werden. Dies ermöglicht die rechtzeitige Planung von Wartungsarbeiten in Abstimmung mit den Betriebsbedürfnissen sowie die Vermeidung von Folgeschäden. Darüber hinaus ist die Instandhaltung am tatsächlichen Bedarf orientiert. Dadurch können Komponenten, die in periodischen Abständen ersetzt wurden, nur bei Bedarf, d.h. wenn durch das Modell ein kritischer Gesundheitszustand einer Anlagenkomponente erkannt wird, gewartet werden. Zusammenfassend können mit diesem Predictive Maintenance Ansatz insgesamt die Kosten für Ausfälle sowie die Instandhaltungskosten reduziert werden.